Core Value
Trust & Accountability
Quality Management. Building Trust Through Accountability.
At Deluxe, we understand we operate in a highly competitive industry. Whilst we have been incredibly successful in keeping our pricing competitive by strengthening mutually beneficial relationships with our suppliers and operating our business as efficiently as possible, we wouldn’t attract and retain the business of the astute builders and developers that we do, without offering exceptional service, quality systems and fastidious installations. That is why quality has always been at the heart of everything we do at Deluxe.
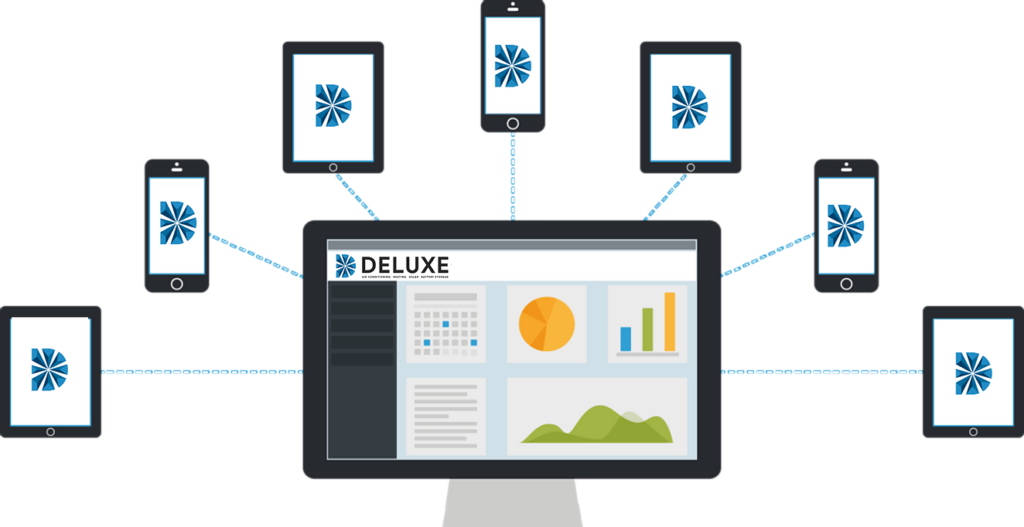
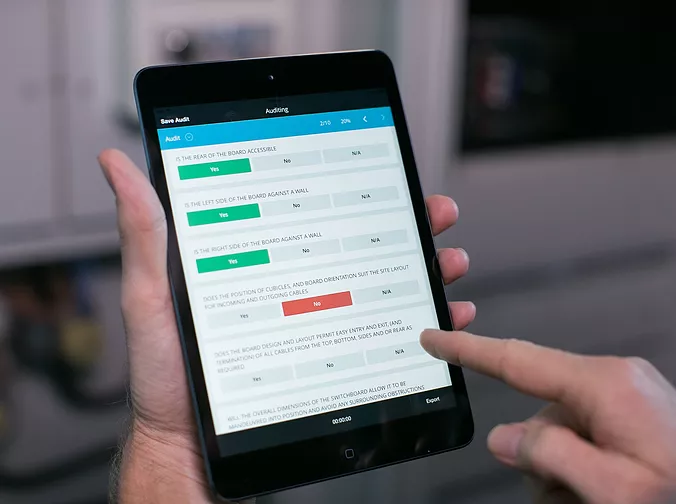
We’re always looking for ways to improve our service, our quality, our systems, our processes and procedures. Looking for ways to better understand our customers, their needs and our own business. Through years of hard work and significant investment in our staff, training and software systems, we believe we’re in a position to offer our customers a level of transparency and accountability that sets the standard of industry best practice that others follow.
To continuously meet our quality objectives and exceed customer expectations we have a rigorous quality management system in place. Within this we have our Quality Assurance, Quality Control, Inspection and Audit activities and responsibilities. Whilst many people mistakenly believe the terms Quality Assurance and Quality Control and
Inspection and Audit are analogous or interchangeable, they’re actually defined differently.
Our Quality Assurance, commonly referred to as “QA”, efforts are focused on our processes and procedures to proactively manage quality and prevent defects. Quality assurance is the part of the quality management system focused on providing confidence that quality requirements will be fulfilled. The confidence provided by quality assurance provides benefits both internally to our management and externally to our customers.
Quality Control is the part of quality management focused on fulfilling quality requirements. While quality assurance relates to how a process is performed or how a product is made, quality control is more the inspection aspect of quality management. An alternate definition is the operational techniques and activities used to fulfill requirements for quality.
Inspection is the process of examining our installations to compare the work undertaken with our best practice guidelines to determine conformity and to make sure that the service being provided to our customers meets our stringent standards.
A section of our Ducted Reverse Cycle Preinstallation
Site Inspection Form
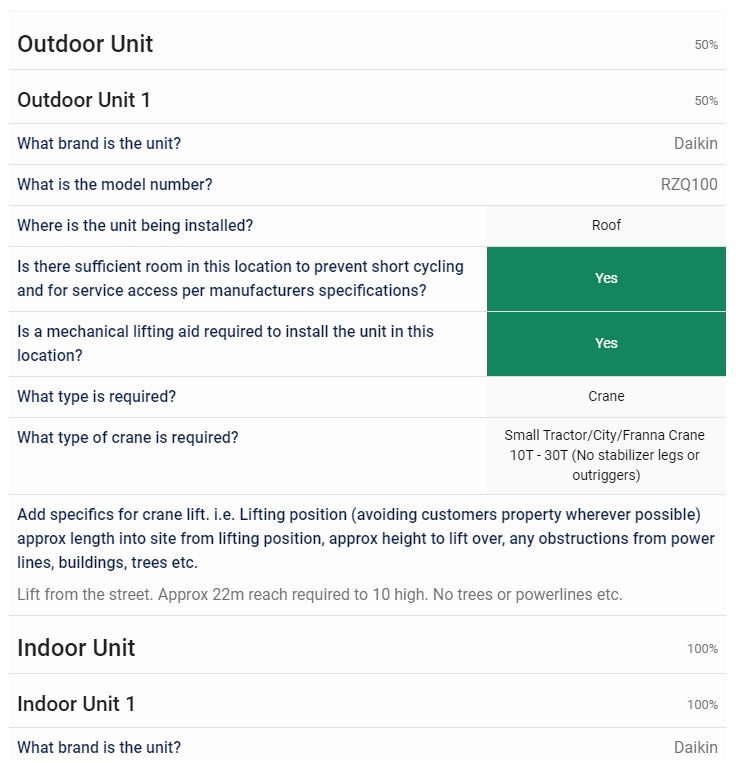
Auditing is part of the quality assurance function. It is important to ensure quality because it is used to compare actual conditions with requirements and to report those results to management. Audit and inspection should not be used interchangeably. Whilst an auditor may use inspection techniques as an evaluation tool, an audit is not used to verify actual acceptance or rejection of a installation. An audit is used to evaluate our processes and controls covering the installation and inspection activities. Audits are also used in environmental, safety and other management systems.
Our experience shows that by creating a quality culture and having a comprehensive inspection and testing system in place, we can consistently produce the highest quality systems for our customers. We also customise our inspection reports to our customers needs where required. Having access to these reports proves to our customers that our processes are of the highest standard throughout planning, installation and commissioning which has allowed Deluxe to develop strong, strategic relationships with many of our customers.
Our quality inspection software provides visibility and insights to help raise quality standards across our organisation. It allows us to inspect sites in minutes, collect consistent data, standardise procedures, send internal and external audit reports, identify failed areas and get problems resolved with the full transparency of sharing this information with our customers.
At Deluxe, our commitment to quality starts long before we arrive at your home or business. We start by carefully recruiting our own in house team of highly experienced trades for their attention to detail and commitment to quality.
On commencement, all new employees undertake full training in our documented installation best practice guidelines.
To ensure a constant focus on quality, we also hold regular “Toolbox Talk” meetings for the whole team where we look at opportunities for improvement based on any real examples identified by our aforementioned rigorous post installation inspections. This process allows us to find and track faults back to their root cause and provides an opportunity to improve our standards, process and procedures to mitigate the likelihood of reoccurrence.
Why should customers put their faith in the team at Deluxe to design, supply and install their next air conditioning, solar or battery storage system?
- Quality Culture. 100% commitment to quality from all employees.
- Industry best practice Quality Management System.
- Quality Inspection Software providing visibility and insights to help raise quality standards across our organisation.
- Mechanisms to identify non conformance with ease, and collaborate/track resolution through traceable followup actions and reports.
- Rigorous processes and procedures in place to ensure that all installations are completed not just to all relevant Australian standards and South Australian regulatory requirements, but to a best practice installation quality standard that we’d expect in our own homes.
- Genuine expert design. As experts in our fields, our team are responsible for the design of thousands of air conditioning, solar or battery storage system that meet our customers comfort, efficiency and energy needs.
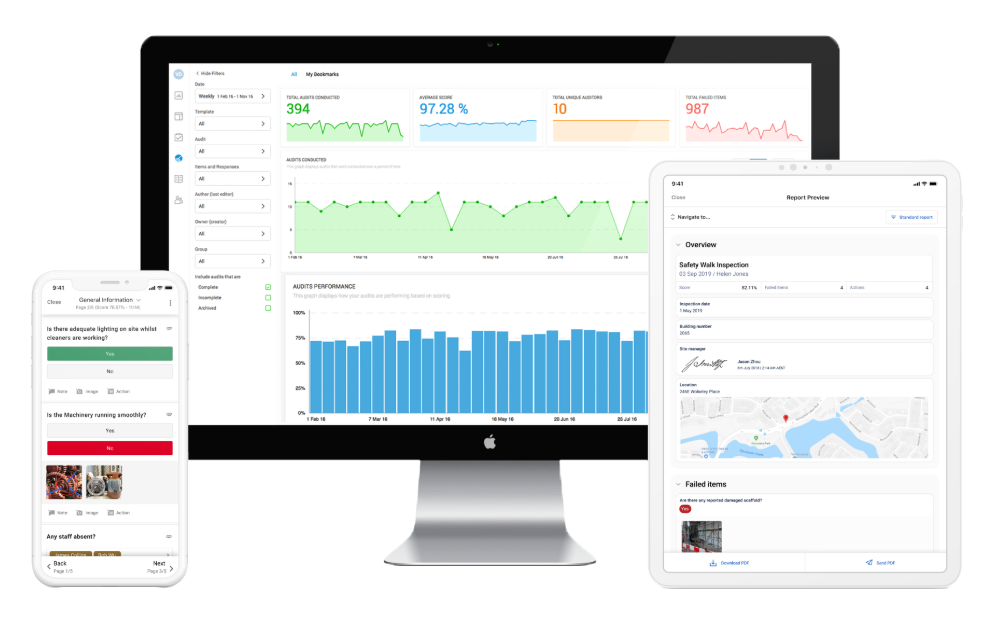
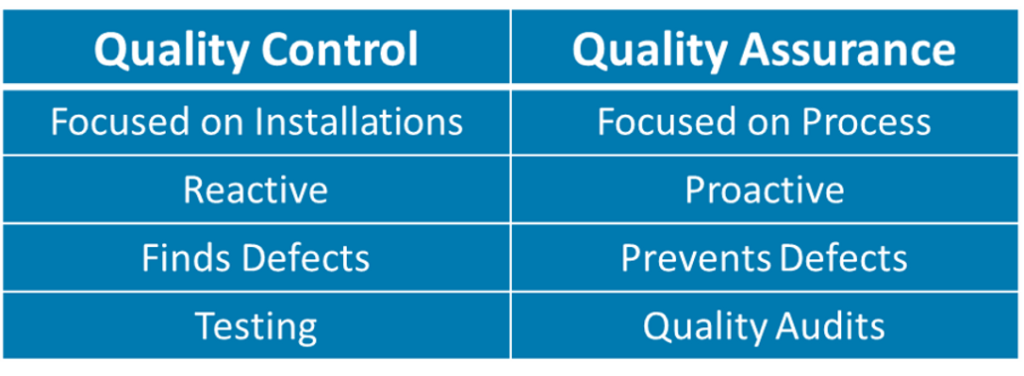